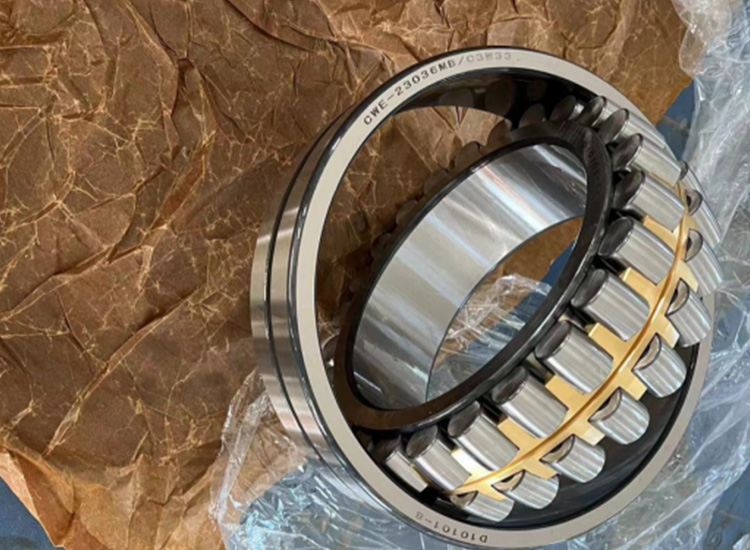
1. Our utilization of domestically renowned special bearing steel brands for raw materials ensures s
1. Our utilization of domestically renowned special bearing steel brands for raw materials ensures superior quality, featuring an oxygen content 10% below and impurity content 10% lower than the national standard. This enhancement significantly augments product wear resistance, resulting in an 8% improvement compared to the general national standard.
2. Beyond furnace testing, our quality assurance measures include random physical sampling and cutting inspection of products from the same batch during heat treatment, thereby guaranteeing the integrity of the heat treatment process.
3. Following the rough grinding of the sleeve and rolling elements, a meticulous 100% acid pickling inspection is conducted to prevent grinding burns and effectively detect defects such as cracks in raw material forging and heat treatment.
4. Our rigorous quality control protocol involves subjecting the sleeve, rolling elements, and finished products to a comprehensive 100% fluorescent magnetic particle inspection, thereby eliminating grinding cracks and subsurface defects.
5. Employing a logarithmic curve for the rolling element raceway enhances the generation of contact edge stress on the rolling surface, resulting in a smoother contact stress curve and a 15% increase in product fatigue life.
6. The utilization of a self-riveting form for the cage enhances its strength, thereby improving impact resistance by 10%.
7. Through super finishing of the rolling surface of the sleeve and rolling elements, achieving a roughness of up to Ra0.1um, we effectively reduce the friction coefficient, operational resistance, and heat generation by 10%.
8. All our products meet precision standards exceeding P5 level, with a 60% reduction in inner and outer diameter tolerances compared to ordinary products, consequently reducing shaft runout by 50%. Most other fracturing pump bearings available have manufacturing accuracy levels lower than P6
9. Stringent control measures ensure internal roundness sizes remain within a mutual difference of 0.02mm, ensuring product interchangeability, enhancing assembly fault tolerance, and reducing maintenance costs.
10. By controlling the mutual difference in clearance within the same group to within 0.025mm, we ensure uniform force distribution on products sharing the same pump crankshaft, thereby achieving balanced product life and effectively increasing the comprehensive service life of fracturing pump crankshaft bearings by 10%.
Our 23036/23038 Pinion bearings are engineered with split type cage
here are reasons below:
1. Split-type cage made of brass with flanges on the inner ring.
2. The impact resistance and load carrying capacity of Split-type structure are 15% greater than that of integral type
3. split-type cage structure can effectively reduce cage wear caused by rolling resistance, effectively improving the cage's wear resistance by 20%.
4. The split-type cage has inner ring flanges for guidance, which makes it more suitable for conditions with significant vibrations, increasing operational stability. The stability of operation in environments with significant vibrations can be increased by 15%.